Engine failure destroys perfect days on the water faster than anything else. Every boat owner encounters these mechanical nightmares, but most breakdowns aren’t random failures – they’re predictable, common boat engine problems with straightforward solutions you can handle yourself.
These seven engine issues cause 80% of all marine breakdowns, yet most boaters waste hundreds on unnecessary repairs because they don’t recognize the warning signs or know the simple fixes. You’re about to discover the exact diagnostic steps and repairs that separate seasoned boaters from weekend warriors calling for expensive tows, giving you the confidence to handle engine troubles before they ruin your time on the water.
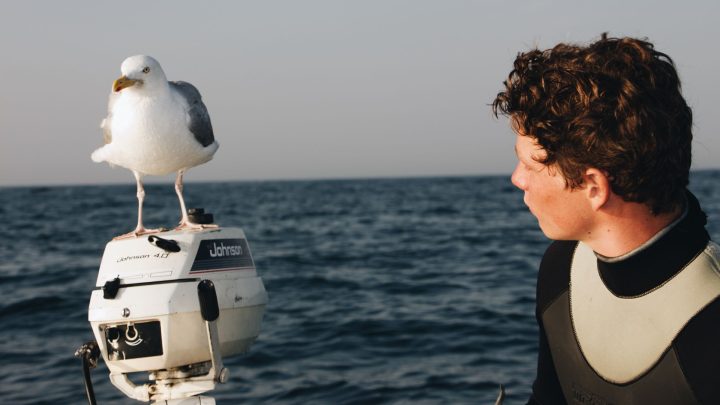
Table of Contents
- Engine Won’t Start
- Overheating Issues
- Poor Acceleration / Power Loss
- Excessive Smoke
- Stalling Issues
- Vibration or Noise
- Fuel System Problems
- Preventative Maintenance Tips
- Common Engine Problems Have Straightforward Solutions
- FAQs – 7 Common Boat Engine Problems
Engine Won’t Start
Nothing kills the excitement of a day on the water faster than turning that key and hearing… absolutely nothing. When your boat won’t start, it’s like your weekend plans just got tossed overboard. Your battery is the heart of the whole operation – a dead or low battery is the most common culprit. You need at least 12.6 volts for a full charge. When your battery’s fine but your engine still won’t fire up, the ignition coil might be the problem, transforming voltage from the battery into a higher voltage needed to create a spark. Your starter motor provides the muscle – clicking noises usually mean the starter solenoid’s trying to engage but failing.
Essential Starting Checks
Start with the absolute basics – many seasoned boaters overlook these simple checks. Verify that the kill switch is properly engaged and your shift lever is solidly in the neutral position. Most boats have safety mechanisms that prevent starting while in gear, even though gauges and lights will work fine.
For battery issues, use a multimeter to test voltage while cranking the engine. If it drops below 8 volts, you’ve got a battery problem – either charge it or replace it entirely. Don’t just check resting voltage; load testing tells the real story. Clean any corroded terminals with a wire brush and tighten connections. You’d be amazed how often crusty, loose connections masquerade as dead batteries.
When dealing with ignition problems, inspect your spark plugs first before assuming the ignition coil is bad. Fouled or carbon-covered plugs can make a perfectly good coil look defective. If you’re getting clicking sounds but no turnover, try the old-school mechanic’s trick: give that starter motor a gentle tap with a hammer while someone else cranks the key. This surprisingly works on older engines with stuck solenoids.
- Check that the kill switch is engaged and the shift lever is in neutral
- Test battery voltage while cranking – replace if it drops below 8 volts
- Clean corroded terminals with a wire brush
- Inspect spark plugs for fouling
- Try tapping the starter motor gently with a hammer while cranking
- Check the main fuse (usually 20-amp)
Overheating Issues
When your temperature warning light starts flashing or that dreaded overheating alarm starts screaming, you’ve got about as much time as it takes to say “there goes my weekend” before serious damage kicks in. An overheating marine engine is like a ticking time bomb – ignore it, and you’re looking at warped cylinder heads, blown gaskets, and repair bills that’ll make your wallet weep.
The brutal truth is that 9 percent of boat fires are caused by engine overheating, so this isn’t just about inconvenience. Your engine is too hot isn’t something you push through – it’s something you shut down immediately and fix. Most overheating boat engine problems boil down to one thing: something’s blocking the flow of cooling water through your system.
Your raw water pump does the heavy lifting, pulling water from whatever you’re floating in and pushing it through your engine’s cooling passages or heat exchanger. When that little rubber impeller inside starts falling apart – and trust me, it will – you’re in trouble. A broken impeller won’t just stop cooling your engine; those rubber chunks can travel downstream and clog up your heat exchanger, creating a domino effect of cooling system failures.
Emergency Cooling System Response
First things first – shut down that engine the moment you see temperature warnings. Check your raw water strainer immediately; it’s usually the first suspect when water flow gets restricted. Unscrew the cover and clean out any seaweed, plastic bags, or debris that’s choking your system.
Next, verify that water is pumping out of your exhaust. You should see a steady stream of water coming out with the exhaust gases – no water means no cooling. If there’s no flow, your raw water pump impeller might be toast. These rubber impellers hate running dry and can self-destruct in minutes without proper lubrication.
Check your heat exchanger if you’ve got an indirect cooling system. Over time, these units can get clogged with scale, marine growth, or debris. Sometimes you can backflush the system to clear minor blockages, but severe clogs might need professional attention.
- Shut down the engine immediately when the temperature warning appears
- Check and clean the raw water strainer for blockages
- Verify water flow from the exhaust outlet
- Inspect the raw water pump impeller for damage or missing blades
- Backflush the heat exchanger if the flow seems restricted
- Check all cooling system hoses for kinks or clogs
Poor Acceleration / Power Loss
There’s nothing more frustrating than mashing that throttle and getting the marine equivalent of a shrug from your engine. When your boat feels sluggish and has no power, it’s like trying to water ski behind a rowboat. Poor throttle response issues can turn what should be an exhilarating day on the water into a lesson in patience and mechanical problem-solving.
Most power loss problems come down to one of two culprits: your engine’s not getting enough fuel, or it’s not getting enough air to burn what fuel it does receive. Think of your engine like a hungry athlete – starve it of fuel or oxygen, and performance goes straight down the drain. Compression loss can also rob your engine of power, but that’s usually a more serious internal problem.
When your carburetor starts acting up, you’ll know it. Dirty or clogged carburetors can’t properly mix air and fuel, leaving you with an engine that stumbles, hesitates, or just plain refuses to accelerate properly. Even the smallest piece of debris in those tiny carburetor jets can cause throttle response issues that’ll make your boat feel like it’s towing an anchor.
Fuel and Air System Diagnostics
Start with the fuel system – it’s the most common power thief. Replace your fuel filter first; a clogged filter restricts fuel flow and creates that frustrating bog-down when you hit the throttle. If you don’t have a spare, pull the filter and clean it thoroughly, making sure to drain any water that’s collected.
Check your carburetor if the fuel filter wasn’t the problem. A dirty carburetor with clogged jets will choke your engine’s performance. Look for gum deposits, varnish buildup, or debris in the float bowl. Sometimes, a good carburetor cleaning with appropriate solvents can restore proper fuel flow and throttle response.
Don’t forget about air flow – inspect your air filter and replace it if it’s dirty or clogged. A restricted air filter creates an overly rich fuel mixture that kills acceleration. Also, check for vacuum leaks around the carburetor and intake manifold, as extra air can disrupt the proper fuel-to-air ratio.
- Replace the clogged fuel filter immediately
- Clean carburetor jets and float bowl of debris
- Check the air filter and replace if dirty
- Inspect fuel lines for kinks, cracks, or air leaks
- Test compression if other fixes don’t improve power
- Verify throttle linkage moves freely and reaches full travel
Excessive Smoke
When your engine starts belching smoke like an old coal-burning steamship, you’ve got a problem that needs immediate attention. Smoking exhaust isn’t just embarrassing – it’s your engine’s way of screaming that something’s seriously wrong under the hood. The color of that smoke tells a story, and learning to read those signals can save you from catastrophic engine damage.
Different smoke colors point to different problems, and ignoring any of them is like playing Russian roulette with your engine. Blue smoke means you’re burning oil, often from worn piston rings or valve seals. White smoke usually indicates unburned fuel or, worse, coolant getting into combustion chambers. Black smoke tells you there’s too much fuel and not enough air, creating that burning oil smell that follows your boat like a guilty conscience.
Oil-related problems are often the culprit behind excessive smoke. When your oil filter gets clogged or your piston rings start wearing out, oil sneaks into places it shouldn’t be. Once oil starts burning in your combustion chambers, you’re not just losing oil – you’re creating carbon deposits that can cause even more problems down the road.
Smoke Color Diagnosis and Response
For blue smoke, check your oil level first – overfilling can cause oil to get sucked into the combustion chambers. If the oil level is normal, inspect your oil filter and replace it if it’s dirty or clogged. Black smoke usually means your air filter’s restricting airflow, so check and clean, or replace it.
White smoke on startup is often normal in cold weather, but persistent white smoke means trouble. Check for coolant leaks and inspect your exhaust system for restrictions. If you smell burning oil along with any colored smoke, shut down immediately and check all oil seals and gaskets.
For diesel engines, a little black smoke under heavy load might be normal, but constant smoking indicates problems with fuel injection, air intake, or exhaust systems that need professional attention.
- Check and adjust the oil level if overfilled
- Replace a dirty or clogged oil filter
- Clean or replace the air filter if restricted
- Inspect the exhaust system for blockages
- Check the coolant system for leaks (white smoke)
- Have the fuel injection system checked (persistent black smoke)
Stalling Issues
Nothing’s more frustrating than an engine that runs fine one minute and dies the next, leaving you drifting helplessly while you try to figure out what went wrong. Stalling at idle is like having a car that won’t stay running at red lights – it turns every trip into a nail-biting adventure you never signed up for.
Most stalling problems happen because your idle circuit isn’t getting the right fuel-air mixture it needs to keep running at low RPMs. When you’re cruising at higher speeds, there’s enough fuel flow to mask small problems, but at idle, even tiny issues become big headaches. Air leaks, dirty carburetors, or incorrect idle speed adjustments can all cause that dreaded engine dies scenario.
The idle circuit in your carburetor is like the engine’s life support system at low speeds. When jets get clogged with debris or varnish deposits, or when vacuum leaks disrupt the carefully balanced fuel-air mixture, your engine simply can’t maintain the steady combustion needed to keep running.
Idle Circuit Troubleshooting
Start by checking your idle speed adjustment – many stalling problems are simply engines that are set to idle too low. Consult your manual for proper RPM settings and adjust accordingly. If that doesn’t help, look for vacuum leaks around the carburetor and intake manifold by listening for hissing sounds.
Clean your carburetor’s idle circuit jets if the engine stalls consistently at idle. These tiny passages get clogged easily and need regular attention. Also, check your fuel system – a weak fuel pump or dirty fuel filter can cause intermittent stalling when fuel demand changes.
Don’t forget the basics: ensure your fuel tank vent is open (a closed vent creates a vacuum that starves the engine) and verify your shift linkage isn’t causing the problem by accidentally engaging the gear.
- Adjust the idle speed to the manufacturer’s specifications
- Check for vacuum leaks around the carburetor and manifold
- Clean carburetor idle circuit jets and passages
- Inspect the fuel pump and filter for proper operation
- Verify the fuel tank vent is open and unobstructed
- Check the shift linkage adjustment and operation
Vibration or Noise
When your normally smooth-running engine starts shaking like a paint mixer or making sounds that would wake the dead, you’re dealing with mechanical issues that can quickly turn expensive. Excessive vibration and noise aren’t just annoying – they’re warning signs that something’s breaking, wearing out, or completely out of alignment.
Most vibration problems come from issues with your prop shaft alignment or worn engine mounts that can’t absorb the engine’s natural movement anymore. Think of engine mounts like shock absorbers – when they fail, every vibration gets transmitted directly to your boat’s hull. Propeller issues like bent blades or debris wrapped around the shaft can also create vibrations that’ll rattle your teeth.
Knocking sounds and rough running usually indicate more serious internal problems, but sometimes the fix is as simple as tightening loose engine mounts or replacing worn rubber isolators. The key is catching these problems early before minor vibrations turn into major mechanical failures.
Mechanical Problem Detection
Start with the easy stuff – check all your engine mount bolts to make sure they’re properly tightened. Loose mounts are a common cause of excessive vibration and are simple to fix. Inspect the rubber isolators in your engine mounts for cracking, hardening, or deterioration.
Check your propeller for damage, debris, or fishing line wrapped around the shaft. Even small amounts of line can cause significant vibration at higher RPMs. Remove the prop and inspect the shaft for straightness – a bent prop shaft needs professional attention.
Listen carefully to identify where the noise is coming from. Squealing often indicates belt problems, while knocking sounds from inside the engine require immediate shutdown and professional diagnosis.
- Inspect and tighten all engine mount bolts
- Check engine mount rubber isolators for wear
- Remove debris or fishing line from the propeller
- Inspect propeller blades for damage or bends
- Check drive belts for proper tension and wear
- Listen for specific noise locations to isolate problems
Related: Electric Boat Motor: The Right Way to Power Your Boat
Fuel System Problems
Bad fuel is like bad food – it might not kill you immediately, but it’ll sure make you miserable until you get rid of it. Contaminated fuel, water in gas tanks, and ethanol-related problems are behind more boat breakdowns than just about any other single cause. When your fuel system acts up, you get sputtering, poor performance, and that sinking feeling that your day on the water just got cut short.
Modern fuel with ethanol attracts water like a magnet, and that water-contaminated mixture separates in your fuel tank, creating a mess that clogs filters and corrodes fuel lines. Debris in fuel tanks – everything from rust particles to algae growth – can turn your pristine fuel delivery system into a clogged nightmare that leaves you dead in the water.
Your fuel tank and fuel separator are your first lines of defense against contaminated fuel, but they need regular maintenance to do their job. When these components fail or get neglected, every drop of bad fuel that reaches your engine becomes a potential problem that can leave you stranded.
Contamination Prevention and Cleanup
Start by draining and inspecting your fuel-water separator – this is usually where contaminated fuel problems show up first. If you see water, algae, or debris in the separator bowl, drain it completely and replace the filter element. Check your fuel tank vent to ensure it’s not allowing water to enter during rain or rough seas.
If you suspect water in your main fuel tank, you’ll need to pump it out and start fresh. Add a fuel stabilizer designed to handle ethanol-blended fuels to prevent future water separation. Consider installing an additional fuel filter if your boat operates in areas with questionable fuel quality.
For fuel line leaks, inspect all connections and replace any cracked or deteriorated hoses. Pay special attention to the fuel lines in the engine compartment, where heat and vibration cause the most wear.
- Drain and replace the fuel-water separator filter regularly
- Inspect the fuel tank vent for water intrusion
- Add ethanol-compatible fuel stabilizer to prevent separation
- Check all fuel lines for cracks, leaks, or deterioration
- Install additional filtration if operating with poor-quality fuel
- Pump out and replace contaminated fuel in the main tank
Preventative Maintenance Tips
The Oil Change Golden Rule
Think of engine oil like your engine’s blood – it’s got to stay clean and fresh to keep everything running smoothly. Most marine engines need fresh oil every 100 hours or once a year, whichever comes first. For brand-new engines, that first oil change comes at just 20 hours to flush out break-in debris.
Fall oil changes are your best bet since you don’t want dirty oil sitting in your engine all winter, collecting acids and contaminants that’ll eat away at internal parts. Used oil turns acidic over time, and letting it marinate in your engine for months is like leaving a ticking time bomb under the hood.
Spark Plug Inspection Schedule
Your spark plugs need attention every 100 hours or every other season – they’re working in a brutal environment with constant heat and explosive forces. When you pull them out, they should have that light brownish color with relatively sharp edges. Always replace spark plugs with the exact manufacturer part number – those little markings contain specific performance attributes engineered for your particular engine.
Creating Your Maintenance Rhythm
Before every trip, spend five minutes checking the basics: oil level, battery connections, fuel tank vent, and water intake for debris. It’s like a pilot’s pre-flight check – these simple inspections catch problems before they strand you miles from shore.
After every outing, especially in saltwater, flush your engine with fresh water for about five minutes. Salt is your engine’s worst enemy, and this simple habit prevents corrosion that can cost thousands in repairs.
Common Engine Problems Have Straightforward Solutions
Most boat engine problems are predictable issues with clear diagnostic steps and practical fixes. The engine won’t start means checking the kill switch and testing voltage under load. Overheating requires immediate shutdown and inspection of the raw water strainer. Poor performance typically involves cleaning carburetor jets and replacing the fuel filter. These seven common problems cause 80% of marine engine breakdowns, but understanding their warning signs provides the ability to diagnose and resolve issues quickly. The five-minute pre-trip inspection routine prevents most problems before they occur.
When your engine shows symptoms, you now know how to identify the cause and implement the appropriate solution rather than relying on costly professional assistance.
FAQs – 7 Common Boat Engine Problems
What is the average life of a boat engine?
A well-maintained boat engine typically lasts 1,500 to 2,000 hours, which translates to 15-20 years for average recreational boaters who use their boats 100 hours annually. Saltwater operation reduces lifespan due to corrosion, while freshwater engines often exceed 2,500 hours. Regular oil changes, proper winterization, and consistent maintenance significantly extend engine life beyond these averages.
What is a common problem with outboard motors?
Fuel system contamination is the most frequent outboard motor problem, caused by ethanol-blended fuels attracting water and creating separation in fuel tanks. This leads to clogged fuel filters, corroded fuel lines, and poor engine performance. Regular fuel-water separator maintenance, using fuel stabilizers, and replacing fuel filters prevent most fuel-related breakdowns that strand boaters.
Why do boat engines break down so much?
Boat engines operate in harsh marine environments with saltwater corrosion, constant vibration, and irregular usage patterns that stress components differently than automotive engines. Many breakdowns result from deferred maintenance, contaminated fuel, and seasonal storage without proper preparation. Unlike cars driven daily, boats often sit unused for months, allowing fuel to deteriorate and seals to dry out.
What are the most reliable boat engines?
Yamaha, Mercury, and Honda consistently rank as the most reliable outboard manufacturers, with Yamaha leading in long-term durability surveys. For inboard engines, Mercruiser and Volvo Penta dominate reliability rankings. However, maintenance quality matters more than brand – a well-maintained older engine often outperforms a neglected newer model. Regular servicing trumps the manufacturer’s reputation for actual reliability.