Of all of the sailing materials found on the modern cruising or liveaboard sailboat, the sailing fabrics that make up the sails and lines may be some of the most space age. Sailing materials have advanced remarkably in the past 100 years, and the progress seems to keep speeding up.
There are still plenty of boats flying their trusty old Dacron sails, that’s for sure. But there are also more and more boats using advanced laminate sail fabrics. So let’s look at the differences and figure out which is right for your boat.
Table of Contents
- What are Sails Made Out Of?
- Sail Material Design, Cut, and Weave
- Picking the Right Sailboat Sail Material
- Modern Sailboat Construction and Materials
- Sail Materials FAQs
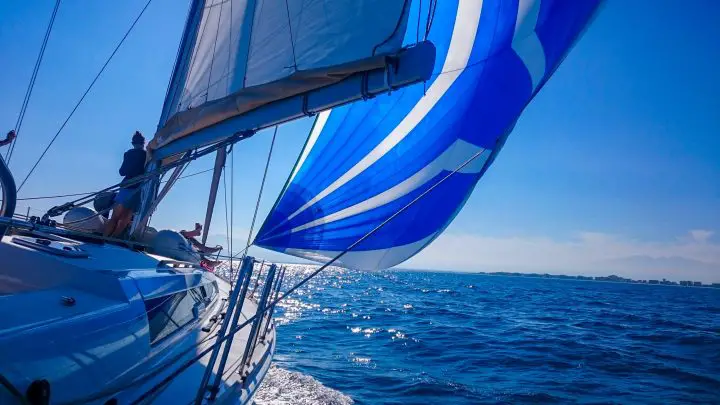
What are Sails Made Out Of?
Sail making material has actually changed dramatically in the last century. For example, the sails of the tall ships of yesteryear were made entirely of natural fibers, yet such a delicate thing is nearly impossible to find on a sailboat today.
But sails have progressed. What are sails made of? The most common material used today in Dacron, a synthetic fiber made of polyester. But progress doesn’t stop there. Today, sails are designed from the ground up in the loft, built fiber by fiber, for that specific application. Today’s racing sails and high-tech and truly marvels of modern engineering.
There are only four basic choices of fabric for sails.
- Natural fibers like cotton canvas, which are very rare now
- Synthetic modern fabric like polyester fiber Dacron, the most common sail material
- Lightweight fabrics like nylon, which is used for spinnakers and downwind sails
- High-tech composite fabrics called laminates, which are used on racing sailboats
Traditional Canvas and “Tanbark”
Before the middle of the 20th century, sails were made of natural fibers (just like everything else on a boat). Cotton canvas was the material of choice but rotting was a major problem. Imagine what would happen to a cotton t-shirt left out in the sun and salt air 24/7/365.
To help them last longer, cotton sails are tanned using tannins from tree bark. Tanbark sails, as these are called, have a reddish-brown color and are more resistant to rot, mold, and mildew.
The modern fabrics that replaced cotton have fixed most of the problems with rot, so real tanbark sails are basically a thing of the past. However, some modern sailcloth options are sold in a tanbark color for sailors who want that traditional look. True cotton sails are not an option for modern sailors. Even if you wanted to deal with the problems and expenses involved, finding a supplier for them would be next to impossible.
If anyone is still flying cotton sails out there, the only purpose would be for historical authenticity. Several museum ships around the world are maintained using original supplies and original materials. They have to source and sew their sails all from scratch.
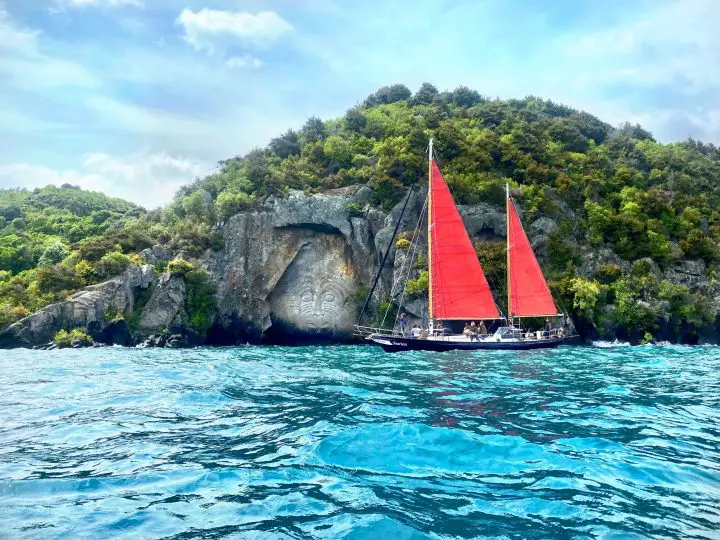
Dacron Sails
Plastics changed nearly everything. Today, it’s nearly impossible to find a product that doesn’t contain some amount of plastic. Most types of sailboats are nearly all plastic when you look closely.
The canvas that most sailors associate with sailing is a woven acrylic cloth commonly referred to by its trade name, Sunbrella. It’s waterproof and extremely resistant to UV damage. It comes in a rainbow assortment of colors, although most boaters seem to prefer blue or green. Grey, tan, and red are also common, but you can find hundreds of options if you’re feeling creative. Sunbrella is used all over the boat–but not for sails.
The cloth used for sails is very similar, but it is woven heavier and more resistant to stretch. It is also most often referred to by its trade name–Dacron. Dacron is white in color 99-percent of the time. But it is also sold in tanbark, a reddish color that looks traditional.
Colored Dacron sailcloth is becoming more common, although it is still rare to see it on the water.
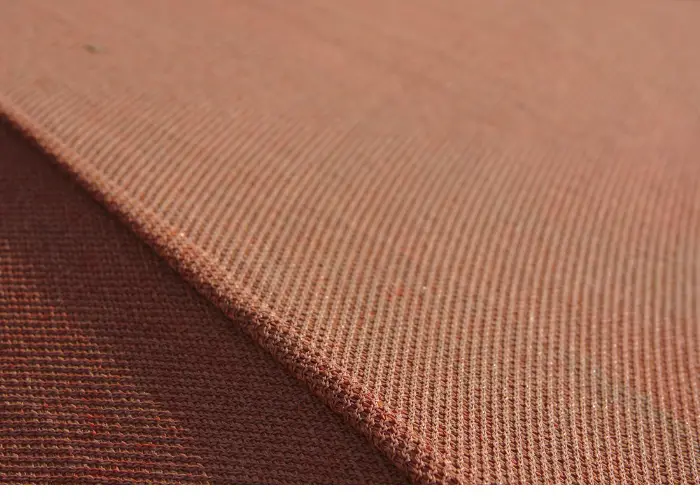
Dacron is the type of sail material you’ll see on nearly every sailboat you find. Dacron comes in various thicknesses or weights. The heavier the fabric, the stronger it is to take on heavy weather sailing. So a storm sail will be built out of heavy-weight fabric, whereas a 155-percent genoa made for light air will be made out of lightweight material.
The design and weight of the sail are matched for its purpose. Most boats are equipped with a set of sails that can do all conditions–but this nets you a “can do everything moderately well” sail. If you want light-air sails, the lighter fabric is then too thin to fly when the wind pipes up. If you want heavy-weather capability, the fabric will be too heavy to fill when the wind is light.
Dacron is still the number one choice for most sailors because it’s widely available, easily repaired, reliable, and affordable.
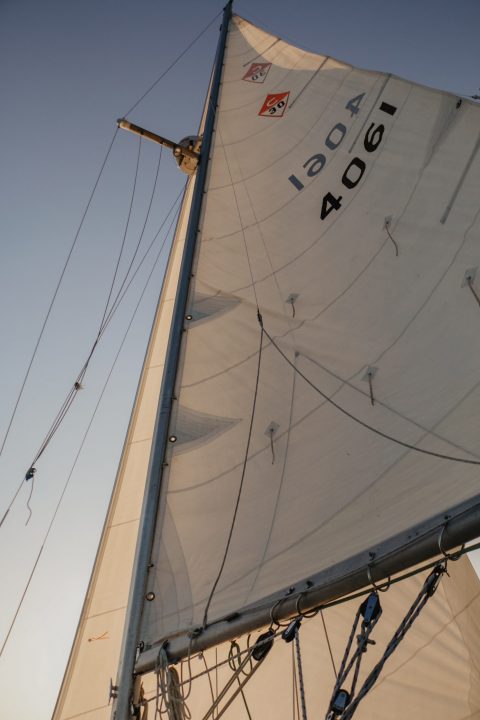
Nylon Sails
More often than not, if you see a colorful sail, it is made of nylon. Nylon is another type of synthetic fiber, but it is woven thin into very soft and billowy fabrics. Many of us own nylon windbreakers or know of the ripstop nylon used in tents, umbreallas, or even parachutes.
When used for sailmaking, nylon is good for light wind sails. It’s not strong compared to Dacron but it is lightweight. That makes it good for catching the slightest puff of breeze. Spinnakers are made of nylon, and since they look and feel like parachutes, sailors often call them “chutes.”
Unlike Dacron, nylon is widely available in any color you could want. Spinnakers are usually creative expressions of the crew or made to match the boat. They often have many colors stitched together in colorful patterns, just like hot air balloons.
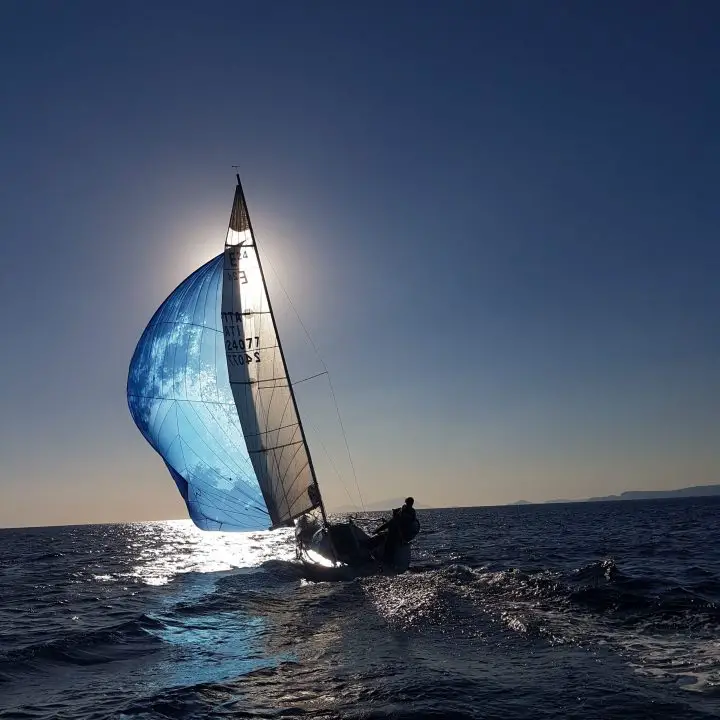
Laminated Sails and Carbon Fiber Sailcloth
The hottest thing in sailing is laminated sailcloth. The word “laminate” refers to a combination of materials stacked together to make a composite structure. For example, our hulls are made of fiberglass laminates. Racing boats have sails that are often laminates made of high-tech fibers and fabrics that offer maximum performance, strength, and sail shape.
Laminate sails start with a Mylar sheet base layer. High-tech fibers are then laid out and glued to this base. Finally, a material called taffeta gives the sail some strength and resistance to chafing. With so many options of materials, all layered one on top of the other, the sail can be precisely the shape the designer intends. Laminated sails are usually black or grey in color, and are sometimes transparent.
Eight different sailing fabrics can be used in laminate sails.
- Carbon fiber sails
- Spectra or Dyneema (Aramid fibers)
- Twaron
- Technora
- Kevlar
- Vectran
- Polyester
- Pentax
Laminated cruising sails offer the best performance and sail shape, but they are extremely expensive and generally not for your average cruising boat. They tend to offer shorter service lives and are more prone to UV damage than Dacron sails.
These high-tech sails can be made in one of two ways. First, the laminate materials may be created in rolls, just like Darcon or any other woven fabric. The sail loft then takes the material and cuts the panels to make a sail. The sail can be cut crosscut, tri-radial, or bi-radial, just like any other.
Alternatively, some lofts are now creating the laminate fabric as they manufacture the sail. This allows them to orient the strongest fibers of the layup in the perfect place to take the load placed on it during sailing. These sails are called load-path sails. North Sails 3Di sails are an example of this super-cool technology.
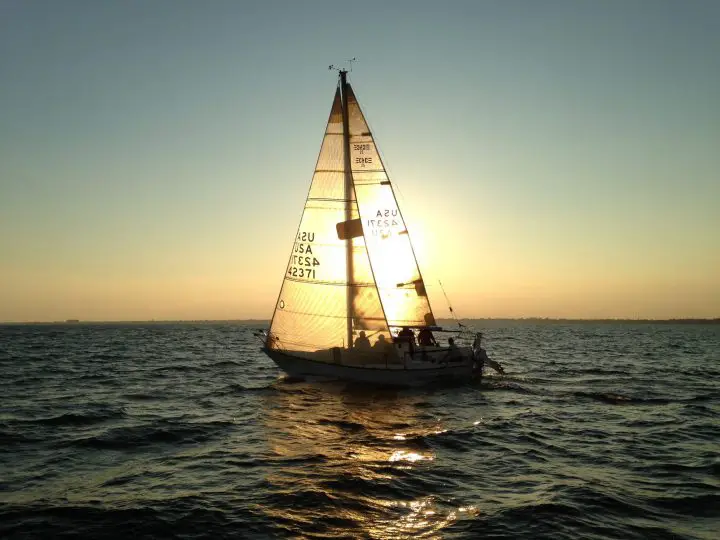
Sail Material Design, Cut, and Weave
The sail manufacturing process is an involved one. Sails are sized for the boat and customized for the cruising conditions in sailing and the style of the sailor at the helm. As a result, there are seemingly endless choices if you want to replace your sails, from the materials used, the sail design and cut to use, the conditions you’ll be expecting, and your goals for your boat performance-wise.
Standard Sail Patterns
Sails are unique in that they must have a specific shape to power the boat. A perfectly flat sail is ineffective. Instead, it should have a curve like an airplane’s wing. This curve, called the draft, must be built-in. Sailmakers cut each piece of the sail with this in mind, and then the completed sail can have as much or as little curve as necessary.
There are three main types of cut that a sail can have to accomplish this–crosscut, tri-radial, and bi-radial. Each type varies in complexity and cost to manufacture and provides a different amount of shape-holding potential throughout its service life.
Crosscut Sails
Most sails you find will have crosscut designs. These sails are cut in strips that run from forward to back at a slight angle. Once the entire sail has been stitched together, reinforcements are added at each corner.
Stretching is a natural part of a sail’s life as it is trimmed and filled with wind. A crosscut sail does not have any extra structure to help it resist stretching, so they are more prone to it than other cuts.
When a sail has been stretched so far that it loses sailing efficiency, it’s said to be “blown out.” When crosscut sails blow out it will be a gradual process as the panels stretch a little bit at a time.
Tri Radial Sails
Tri-radial cut sails have a distinctive look to them. The panels that make the sail are smaller triangles that radiate from each sail corner. Tri-radial sails are made of more panels than crosscut ones, so there is more potential for a knowledgable sailmaker to fine-tune the design. This can result in a more efficient sail shape.
The extra seams in the sail also reinforce the sail overall. This results in a sail that doesn’t stretch as much over time. But once it does go, it is likely to blow out and needs replacement quickly.
If you’d like to see a detailed look at how the pieces of a tri-radial sail fit together, check out this DIY video from Sailrite. Sailrite sells sew-your-own sail kits, with the parts cut from CAD-designed plans.
Biradial Sails
A bi-radial sail is just like a tri-radial, except that the panels that make the design come from only two corners–the head and the clew.
Load-Path Sails
Load path sails are built piece by piece in the loft using composite laminates. Instead of starting with sheets of material, the loft starts with the raw materials that will make the completed sail. Then, it is glued together into the final shape, with strong fibers reinforcing its built-in shape.
Weave Patterns in Sailboat Sail Materials
Not all fabrics are woven together in the same way. Dacron can be woven in multiple ways, and your sailmaker must know how to combine the right weaves with how the fabric is cut for the sail. The weave is designed to provide strength in one direction and shape in another.
Quite often, the difference in price between two similar-looking pieces of Dacron comes down to the weave. This is because the weave gives the Dacron “tenacity.” High-tenacity Dacron fabrics are best for cruising sails because they stretch less and distribute the load evenly over the sail.
It’s also important to consider the weave of the material when choosing the cut of the sail. For example, a cloth that works for crosscut sails will not be best for a radial cut sail. In addition, some manufacturers weave the Dacron with high-tech fibers, like Dyneema, for extra strength.
The important thing to know is that the weave of the sail cloth fabric you chose must match the cut of the sail’s panels. In other words, you can’t use the fabric from a tri-radial sail to make a crosscut sail or vice versa.
Picking the Right Sailboat Sail Material
For the amateur sailor, sorting through the dizzying array of choices of sailboat sails material is daunting. The flashy racing sails and load path sails are tempting, but are they worth it?
The truth is, Dacron is still popular for a reason. If you’re lucky enough to be outfitting a $500,000 aluminum sailboat, buying the best of the best only makes sense. But most of us are on a budget when outfitting our boats.
What’s more, will you notice the difference between a high-tenacity high-end Dacron compared to a laminate? The answer is probably no on an older, heavy displacement cruising boat. But, on the other hand, on a high-performance catamaran or trimaran, it might be well worth the investment.
The Most Crucial Part of a Sail Design
Here’s a video from renowned sail loft Precision Sails discussing the most important factors when choosing your next set of sails.
Modern Sailboat Construction and Materials
Our boats have progressed a lot since the wooden-hulled and canvas-sailed ships of the past. Revolutionary new materials mean boats and sails that resist water, pests, and UV damage. As a result, years are added to the life of parts, and maintenance costs are reduced in the process. And if there’s one thing that every boater can agree on, it’s that most time sailing and less time doing maintenance is good news.
Sails are a major investment. For the average boater, a set of new sails should last ten or more years. Unless you’re planning on circumnavigating or racing competitively, most people never have to replace a set of sails. If you are faced with the choice, be sure to consult with a knowledgable sail loft that is familiar with your boat and your goals for it.
Sail Materials FAQs
What are the materials used in sailing?
Sailboat sails are usually made of Dacron, a synthetic fabric made of polyester. It is very heavy, resists tearing, is waterproof, and resistant to UV damage.
What is the best material for a sail?
Nearly all sails on cruising boats are made of Dacron, a trade-name for polyester fabric. Dacron is long-living and resistant to water, UV damage, and rot.
What material are sailboat sails made of?
The most common sail material is Dacron, a type of polyester fabric. Alternatively, racing boats or yachts may have laminate sails made of high-tech materials like Kevlar or carbon fibers.
Is boat sail material waterproof?
Yes, the materials used in sailmaking do not absorb water. Dacron is the most common material, and it is extremely water-resistant.